ZT-4006B UV Ultraviolet Accelerated Aging Test Chamber
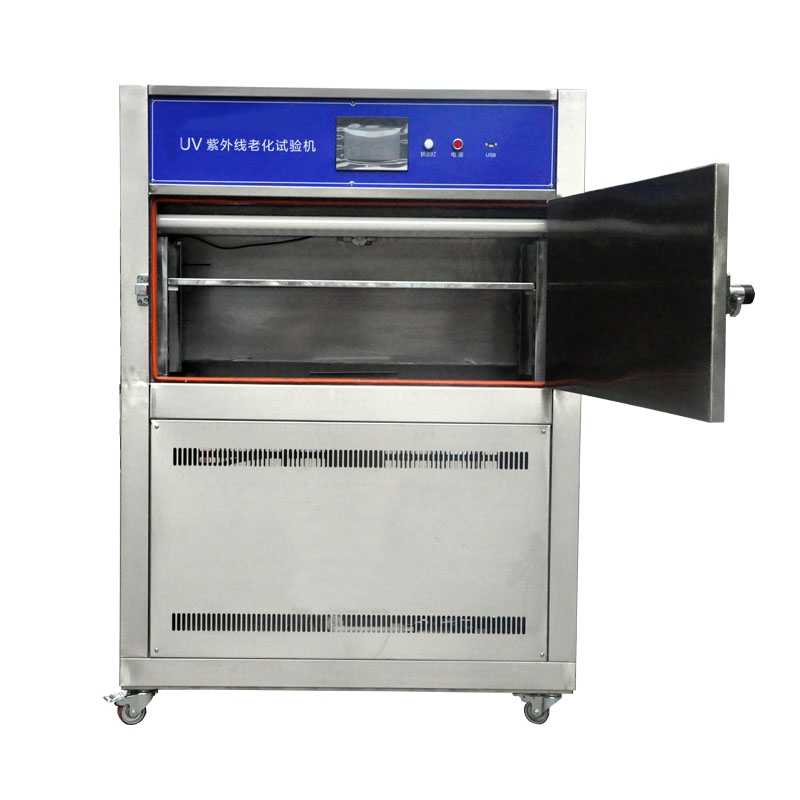
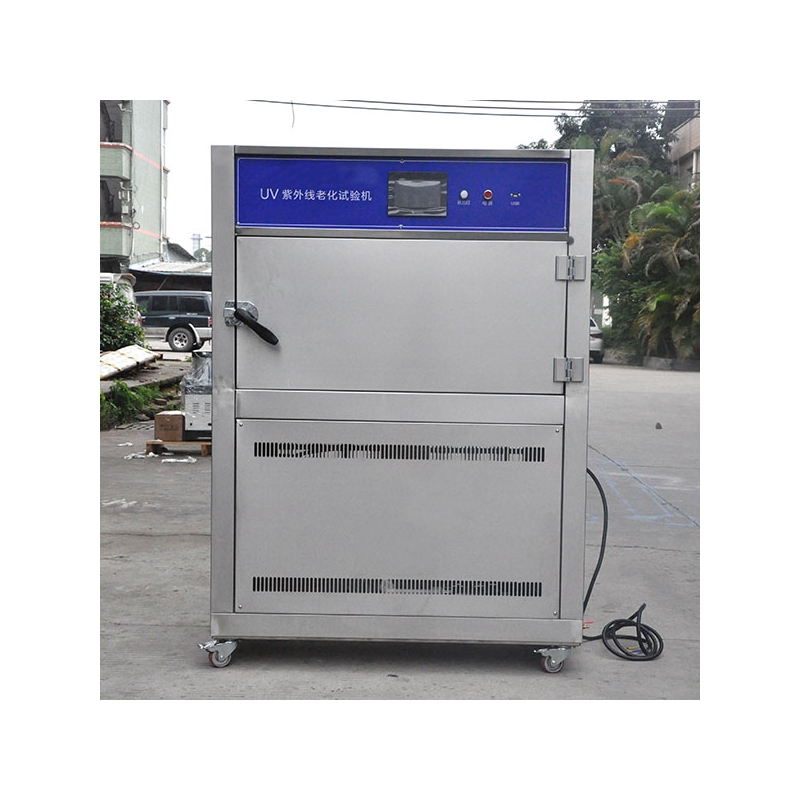
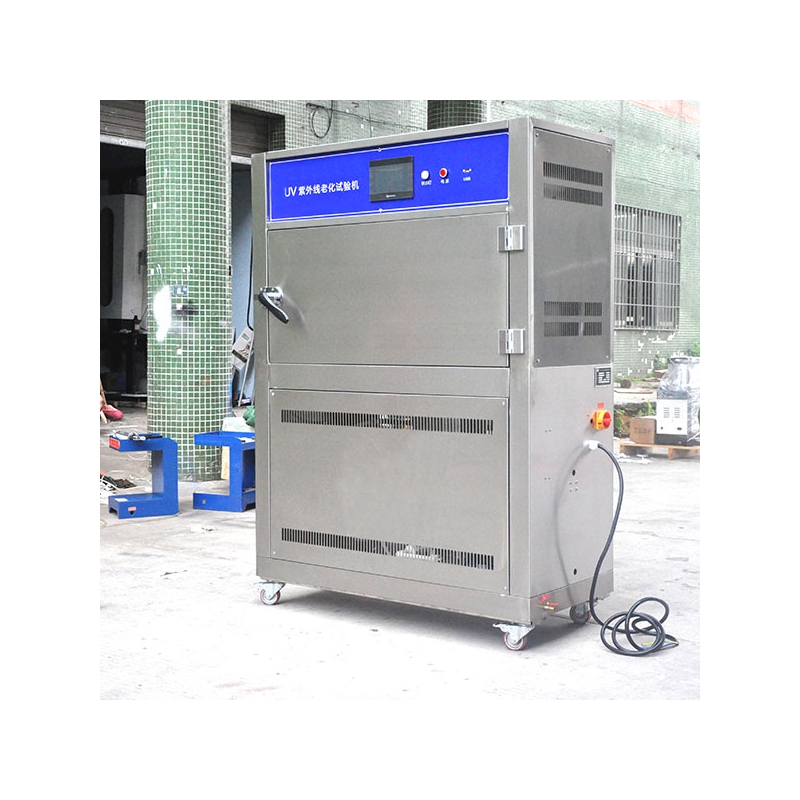
UV Ultraviolet Accelerated Aging Test Chamber
Technical parameter:
Name |
UV Accelerated Weather Resistance Aging Test Chamber |
Bulb number |
UV Lamp 4, spare lamp:4 |
ATLAS,UVA340,UVB313,UVC351) |
|
Ultraviolet tube |
UV wavelength 280~ 350nm |
Recorder |
Option |
Radiometer |
Option |
UV temperature |
RT+10 ℃ to 75 ℃ |
Temperature uniformity | ±3°C |
Temperature fluctuation |
±0.5°C |
Humidity range |
≥75%RH |
Inner center distance of lamp tube |
65~70mm |
The distance between the sample and the center of the lamp tube | 55mm |
Water spray |
0.8MM spray hole, 8 nozzles |
Water and consumption |
distilled water, 8 liters / day |
Volume |
120 * 50 * 60cm (W * D * H) |
Outer box room size |
145 * 85 * 165cm (W * D * H) |
Weight |
150kg |
Power |
1 ψ , 120V/60Hz,16A or 230V/50Hz, 9A,1800W(max) |
Equipment summary:
Ultraviolet Accelerated Aging Test Chamber can simulate the sun, rain and dew to damage the material, UV using UV lamp simulate the effect of sunlight, cold rain and dew. Being tested materials are placed in a certain environment which the light and moisture are alternating. The materials are tested for several days or weeks, you can know the damage of material at outside for several months or several years, Damage types include: bleaching, discoloration, loss of light, powder, crack, turbidity, bubble-based, embrittlement, strength decline and oxidation.
Main functions:
UV test machine, the UV lamp can simulate the effect of the sun, condensation and water spray system can simulate the effect of rain and dew. the temperature can be controlled at the process of testing. A typical test cycle is usually testing at UV radiation of high temperature and the 100% humidity at dark; Typically used in paint and coatings, automotive, plastic products, wood products, glue, etc.
Corresponding standard:
Accord with ASTMG53-77, ASTM D4355
Applicable industries:
Ultraviolet Accelerated Weather Resistance Aging Test Chamber is widely used in paint, resins, plastics, printing and packaging, aluminum, adhesives, auto, cosmetics, metals, electronics, electroplating, medicine, etc.
Main feature:
1.Simulated sunlight
The damage of material durability is mainly caused by the sun‘s ultraviolet ray. We use UV lamps to simulate sunlight in the ultraviolet part of the short-wave, it produces very little visible or infrared spectral energy. We can choose according to different testing requirements of different wavelengths of UV ultraviolet light, because each lamp in the total energy and wavelength of UV radiation are not the same. Usually, UV lamp can be divided into two kinds of UVA and UVB.
2.UV lamp type
UVA-340 lamp: UVA-340 lamps can simulate short-wave UV light in the sunlight excellently, ie sunlight from 365nm to 295nm cutoff wavelength.
UVB-313 lamps: UVB-313 lamps are usually issued by short-wave UV radiation than the Earth‘s surface in the strong solar ultraviolet radiation, which can speed up the greatest degree of material aging.However, the lamp may have caused some of the material does not meet the actual damage.UVB-313 lamp is mainly used for quality control and research and development, or on the weather ability of materials strong run the test.
UVA-351 lamp: Simulation of UV sunlight through windows, it is the aging of indoor materials for testing the most effective.
3.Moisture condensation environment
In many outdoor environment, the material wet day time can be up to 12 hours.The results show that this result is the main factor of outdoor wet dew, not rain.UV condensation through a unique function to simulate the outdoor wet erosion.Condensation during the test cycle, the test chamber at the bottom of the reservoir, water is heated to generate super heated steam to fill the entire test chamber, hot steam to the test chamber maintained at 100% relative humidity, and maintain a relatively high temperature.Sample is fixed in the test room wall, so the test sample surface exposed to ambient air in the test room.The outward face of the sample exposed to the natural environment has a cooling effect, leading to internal and external surface of the sample with temperature, the temperature difference causes the appearance of the sample in the whole process of condensation cycle, the test surface always have condensation of liquid water generated.
Because exposure to humid outdoor exposure time up to ten hours a day, so a typical condensation cycle usually lasts several hours.UV offers two moist simulations.The most widely used is the condensation method, which is to simulate the best way of outdoor wet erosion.All models can be run UV condensation cycle.Conditions because some applications require the use of water spray in order to achieve practical results, some condensation cycle UV models can be run either run the water spray cycle.
4.The temperature control in each cycle, the temperature can be controlled at a set value.At the same time the board can monitor the temperature of the thermometer.Higher temperature can accelerate the aging process, while temperature control for reproducibility of the test is also very important
5.The water spray system for some applications, the water spray can better simulate the end use of the environmental conditions.Water spray in a simulated drastic changes in temperature and rainfall caused by the thermal shock or mechanical erosion is very effective.Conditions in some practical applications, such as sunlight, heat together the stroke of showers dissipated rapidly, the material will be dramatic changes in temperature, thermal shock, thermal shock for many materials, this is a part oftest.UV water spray to simulate thermal shock and / or stress corrosion.Sprinkler system with 12 nozzles, each side in the test room of 6; sprinkler system can run a few minutes and then shut down.This short cooling water samples quickly and create a thermal shock conditions.
6.Irradiation intensity control: optional matching light intensity control option available to accurately type and reproducible results; light intensity control system allows users to set different requirements of different test light intensity. Feedback loop devices through its precise control of light intensity; but also can extend the life of fluorescent lamps.
Main structure:
1. Box made by numerical control equipment, advanced technology, smooth lines,
elegant appearance
2. Box material is 1.2mm thickness 304SUS stainless steel
3.The air duct in the oven adopt single-cycle system, with import of axial flow fan, To improve the air flow, heat ability, greatly improved the uniformity of the temperature in the cabinet
4. Tube: Special uv lamp, 2 rows, 8PCS, 40W/PC
5. Lamp Lifetime: more than 1600h
6. Water supply and consumption:Tap water or distilled water about 8L/day
7. Both sides were installed in the studio 8PCS UVA or UVB lamp
8. Heating method: Bladder tank type heating, heat up fast, temperature distribution uniformity
9. Tank cover:double flip, easy shut down.
10. The tank water level automatic filling water, prevent damage of heat pipe air to burn.
11. Sample frame is made from stainless steel or aluminum alloy.
12. Machine bottom using high quality PU wheel fixed
13. Drainage system using U type drainage device
14. The test sample surface with uv light plane in parallel
15. Internal installation of automatic sprinkler spray system, the water pressure is adjustable